Methods of reducing no-load loss
Writer: Hengfeng you electric Time:2022-01-12 views:times
After analyzing the no-load loss, the hysteresis loss and eddy current loss of the iron core are mainly determined by the silicon steel sheet manufacturer, and the additional loss is determined by the transformer manufacturer. The magnetic flux density of the iron core is an important parameter affecting the no-load loss of the transformer iron core. Therefore, to reduce the no-load loss, it is necessary to make the magnetic flux density distribution of each part of the iron core tend to be uniform and reduce the magnetic flux density at the corner of the iron core on the premise that the useful section of the iron core remains unchanged.
1. The staggered joint is changed to the third-order joint
Because there is a gap in the joint of silicon steel sheet of transformer core, the magnetic flux suddenly increases through the joint, so the magnetic flux has to bypass the gap of the joint and enter the adjacent laminations through the sheets, and then part of the magnetic circuit increases, and the magnetic resistance across the sheets increases, which also increases the magnetic density of the adjacent laminations, resulting in the increase of no-load loss and excitation capacity.
The more the number of transformer core joints, the lower the partial loss in the joint area, but the smaller the decrease of partial loss. The number of core laminations, the working hours of silicon steel sheet shearing and core lamination, and the process difficulty of core lamination will increase with the increase of the number of joints.
In practice, considering that with the increase of the number of stages, the working hours of silicon steel sheet shearing and iron core lamination increase accordingly, and the lamination process becomes worse. It is considered that if the three-level joint is selected and the appropriate sheet type is selected, only one sheet type is added to the core column, the process complexity is slightly increased, and the magnetic function is significantly improved. The three-stage joint of the iron core is made of three types of laminations in turns. According to the technological level of metallurgical electric repair enterprises and the magnetic function data of joints, the selection of three-level joints is an ideal choice to improve the staggered joint iron core.
Taking s9-800 / 10 and s9-1000 / 10 power transformers as examples, the same planning scheme, structure and materials are selected for the same transformer, and different lapping methods are selected for the iron core. Among them, 4 sets of 800kVA are selected with staggered joints, 3 sets are selected with three-level joints, 2 sets of 1000KVA are selected with staggered joints, and 3 sets are selected with three-level joints.
Through the experimental data, it can be concluded that the no-load loss of the three-stage joint is about 7% ~ 8% lower than that of the staggered joint when the section of the iron core column is unchanged. Only one sheet type is added to the core column for the three-stage joint, and the working hours for shearing silicon steel sheet and stacking iron core are slightly increased, but the results are obvious.
2. Reduce the overlapping width of iron core and reduce the no-load loss of iron core
At the corner of the core lamination, the overlapping width of the joint area between the core column and the cross yoke has a certain impact on the no-load function of the transformer. When the overlapping area is large, the area through which the magnetic flux passes increases accordingly, and then the no-load loss increases. According to the iron core model experiment, the no-load loss of 45 ° joint will increase by 0.3% for every 1% increase in overlapping area. To reduce the no-load loss, it is necessary to study and select the best lap area on the premise of meeting the mechanical strength.
Changing the connection area of the laminated tower of the iron core can reduce the size of some triangular holes in the iron core, reduce some magnetic flux density at the triangular holes, and reduce the no-load loss of the transformer. The original angle of iron core lamination of distribution transformer in our company is 10mm, but it has been changed to 5mm, which has achieved certain consumption reduction effect. The outlet angle of the iron core lamination is changed from 10mm to 5mm, so that the cross-sectional area of the triangular hole at the corner of the iron core is increased, and the magnetic flux density at the triangular hole is bound to decrease.
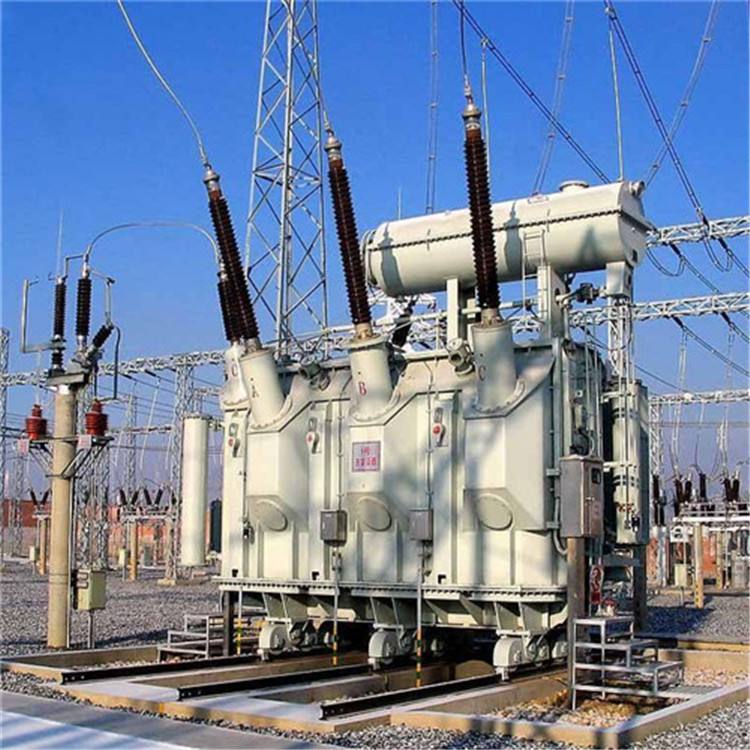
3. Reasonably select the iron chip width, reduce the iron core angular weight, reduce the iron core material and reduce the no-load loss
The no-load loss of iron core is related to the unit iron loss of iron core and the component of iron core, and the angular weight of iron core is a part of the component of iron core. Therefore, the angular weight of iron core not only affects the cost of transformer, but also directly affects the no-load loss of transformer.
The preconditions for discussing the rules of iron chip width selection and iron core angle weight change are as follows:
(1) The stages of the iron core must be equal.
(2) The diameter of the iron core is D, and the main stage sheet width of the iron core is selected according to D minus 5mm or 10mm. Different core diameters are formed by the sheet width and stack thickness at all levels. The maximum first-order difference between the two cores is controlled below + 0.3mm, that is, the winding package cannot be affected because the core diameter exceeds the difference.
(3) The effective cross-sectional areas of iron cores with different sheet shapes are equal in theory.
The purpose of this is to ensure that the same flux density is selected and the same unit iron loss is obtained.
(4) The slice width and stack thickness of the core column section are necessary to be in common with the core yoke section.
In the planning process, when the appropriate core diameter is confirmed and the sheet width of the main stage core is selected, it is recommended that the effect of sheet width D minus 10mm is better than that of D minus 5mm. Its advantages are as follows:
① The slice width at all levels decreases step by step;
② Under the condition of ensuring that the useful cross-sectional area of the iron core is equal, the angular weight of the iron core is reduced;
③ The height of the iron core is reduced by 10mm, the overall height of the oil tank is also reduced by 10mm, and the materials of the transformer are also saved